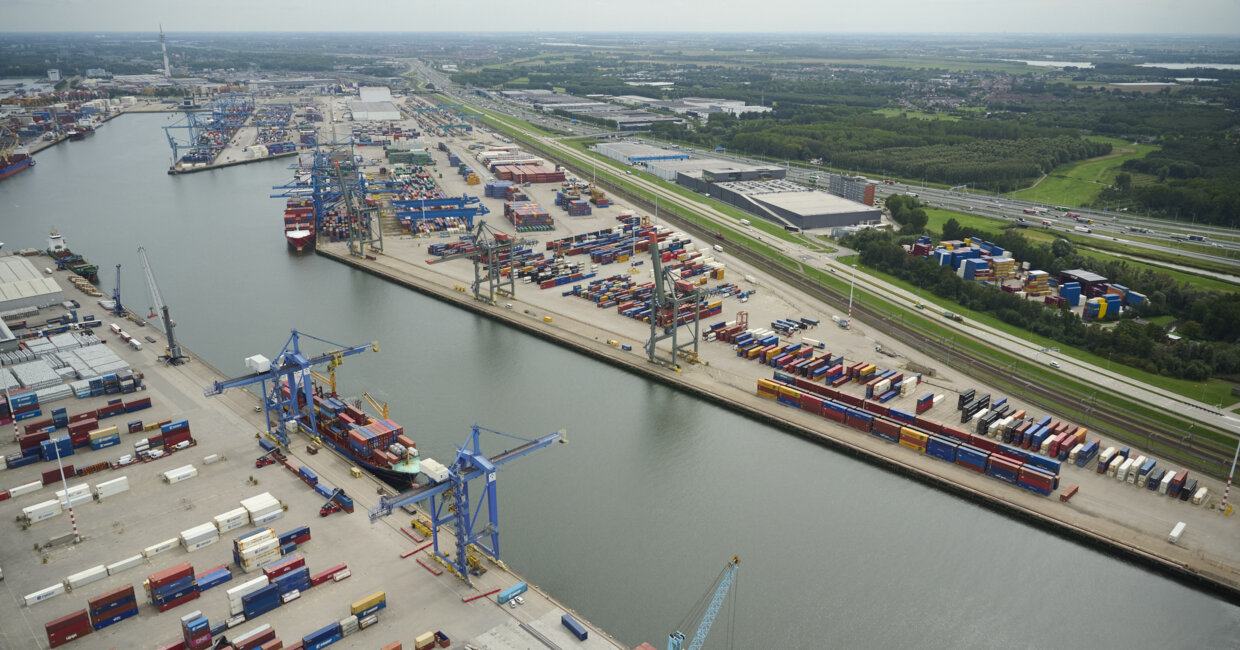
Milestone for cutting CO2: Kalmar’s 600th hybrid straddle carrier to be welcomed in Rotterdam
Give and take. It’s an expression we’re all familiar with, perhaps because it is so universally applicable. To gain something here, you need to lose something there. We can’t always have our cake and eat it. Something has to give.
So when a hybrid model of machine can offer reduced costs and reduced emissions compared to its diesel counterpart, the logical question would be: what do you give up? In the case of the Kalmar Hybrid Straddle carrier, the answer is: nothing.
Thanks to its regenerative power system and efficient diesel engine, the Kalmar Hybrid Straddle Carrier can reduce fuel costs and on-site emissions by as much as 40% – and with no compromise on performance compared to its diesel predecessors.
A solid business case: fuel savings equal cost savings
“The product was ahead of its time when it was invented 10 years ago,” explains Marko Hopeaharju, Head of Horizontal Transportation Solutions at Kalmar. He remembers that hybrid technology was slow to catch on in the cargo shipping and handling industry. That hesitation to adopt new technologies is often just a case of needing proof that it works.
“It started with some of our customers, and they convinced other customers that hybrid technology works.” That in turn has led to exponential growth of Hybrid Straddle Carrier sales. One-and-a-half years ago, we were celebrating the sale of our 400th Hybrid Straddle Carrier here at Kalmar. Now, we’re already celebrating the sale of our 600th. “Today, the business case is solid. Fuel savings equal cost savings,” Marko points out. “Some are still buying combustion engine models, but for many, it’s now a question of: why buy a diesel machine when a hybrid has proven to work?”
"Today, the business case is solid. Fuel savings equal cost savings."
With today’s hybrid technology as advanced as it is, it is hard to make a case for all-diesel machines – especially when the level of performance is the same. The hybrid straddle carriers may require an initial investment, but the cost savings from reduced fuel consumption soon start to pay that back. Even from a maintenance perspective, the hybrid straddle carrier is ahead of the game. The diesel engine that makes up one half of the hybrid power system is small and easy to maintain. That engine charges the other half of the system: a compact, high-capacity battery that is also easy to maintain – and boasts a long lifespan.
The hybrid straddle carrier has a proven track record of success. For one such case, we can look to Europe’s largest dedicated shortsea shipping hub – and the owner of Kalmar’s 600th hybrid straddle carrier.
Hybrid straddle carriers serving a key European hub
“I don’t think we bought all 600,” laughed Arno Storm, CEO of Rotterdam Shortsea Terminals (RST). “But of course, that’s an honor. I’m very happy to welcome the 600th strad.” RST serves around 15 shipping lines and handles as much as 800,000 containers a year. Their operations have a strong focus on two key areas: enabling intra-European trade, and eco-friendly operations. The hybrid straddle carrier supports both of these endeavors.
Hybrid straddle carriers now make up half of the straddle carrier fleet at RST, and they aim to replace the older diesel models in the coming years. “From a financial point of view – but also from an environmental responsibility point of view – we saw that those hybrid machines were way more efficient than our old fleet.”
"From a financial point of view – but also from an environmental responsibility point of view – we saw that those hybrid machines were way more efficient than our old fleet."
What makes the hybrid straddle carrier a good fit for RST? After sending out a request to several manufacturers, they compared the responses on the basis of two key metrics: cost and the amount of CO2 reduction that the new equipment would enable. “For us, it was clear that Kalmar was the ideal company,” Arno says.
For RST, the hybrid straddle carrier lives up to its promise: reduced cost and reduced emissions without compromising performance. And that promise is the conjuncture of enhancing business operations and looking out for the planet – sustainable practices can serve both of those objectives. On top of that, Arno has identified a more subtle effect within the company that has come about since RST started its journey to CO2 neutrality.
“It also gives a very positive vibe within our company,” Arno explained. “A lot of people here are mums and dads, and they feel responsible for our planet. Now they can also play a role in reducing CO2.”
“Especially young people who are now entering our company – they found it very, very important. They also look at our website, they look at our CSR report and they say ‘hey, this is a company that I would like to work for.’”
It looks like we can add “morale” and “recruitment” to the aspects of business that can be enhanced by going green.
Next step: going all-electric?
RST aims to achieve net-zero CO2 by 2030. Today, their fleet of hybrid straddle carriers have slashed emissions. Not only do they burn less diesel than their older straddle carriers, but they are also HVO compatible. RST have now decided to use the vegetable-based fuel with their hybrid straddle carriers as it produces 90% less CO2 compared to diesel.
But to reach the net-zero goal, there will eventually be a need to start the transition from hybrid to the next iteration of the straddle carrier, such as an all-electric model. “As soon as we're entering that period in time, we have to make a decision on the second batch of straddle carriers,” Arno said. “So we are very eager to stay connected to Kalmar and to learn from their experience and their development.”
“The transition to all-electric is a big infrastructure challenge,” Marko notes. But while the need for that additional infrastructure may give pause to some customers, Marko is optimistic about how the technology is developing. “The transition from a hybrid straddle carrier to an all-electric one is made easier by the fact that some components are the same. In some cases, it’s as simple as changing the engine unit with a battery unit.”
"The transition from a hybrid straddle carrier to an all-electric one is made easier by the fact that some components are the same."
Kalmar continues to invest in new power technologies, and an all-electric straddle carrier is one prominent alternative. It’s already a proven solution and can be implemented step by step, but industry-wide adoption may still take years.
Related articles
Further reading
Subscribe and receive updates in your email
Subscribe