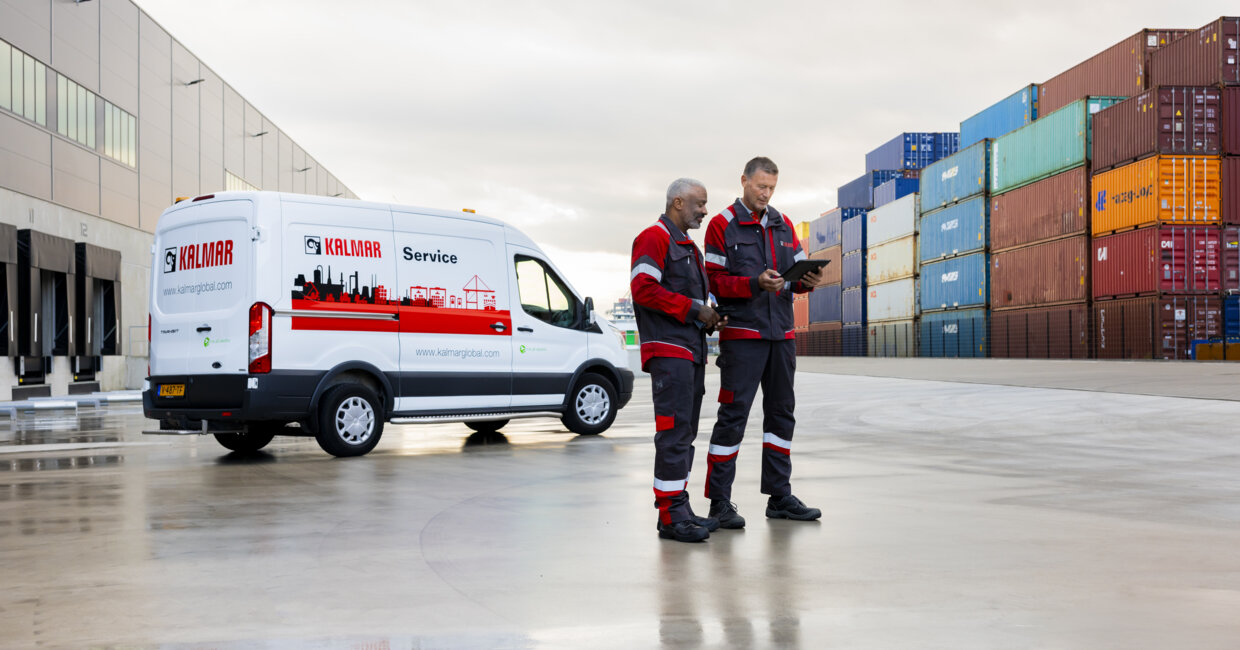
Flexibility and peace of mind: Finding the right maintenance model for your operations
Equipment maintenance is a major investment for port operators, logistics service providers and industrial companies. Maintenance is required to ensure safety, minimise downtime, maximise return on investments, reduce operational risks and improve financial predictability. But what is the best way to organise your maintenance operations – and what options are available?
"Maintenance is a core part of any mechanical activity," says Svante Alveronn, VP, Service Solutions, Kalmar. "You want to ensure you get the maximum lifetime and performance from your equipment, so ultimately your maintenance activities will determine the return on your fleet investment. Also, both safety and energy consumption depend on maintenance, so the impact really extends to every level of operations."
In-house or external?
How, then, should terminal operators or other companies in the logistics industry organise the maintenance of their fleets? The basic choice is between two different philosophies, both of which have their respective merits. Should you have your maintenance done by an in-house team, or sourced from a trusted external provider? And is it better to go for an ongoing maintenance contract, or just order external services when needed?
"In-house, fully contracted and on-demand maintenance models all have their specific benefits, so essentially the question is, do you want maximum financial flexibility, or complete peace of mind?" says Svante Alveronn. "At Kalmar, we have recently restructured our own offering, providing three different levels of service that accommodate any maintenance approach. These range from Essential Care maintenance contracts that cover the basic scheduled service tasks and inspections for equipment, to Complete Care full-service maintenance agreements and flexible On-demand Care services. It's all about providing the customer with the type and level of service that is right for them."
"The optimum maintenance strategy depends on the specific business model of each terminal or operator," adds Timo Elo, Solution Business Development Manager, Service Solutions, Kalmar. "There are many different ways to get the right balance for your operations. However, one of the major benefits of maintenance contracts is that they can enable a more predictive approach to maintenance."
Predictive maintenance is one of the key elements for the successful operation of cargo handling equipment. In addition to manual checks at predetermined service intervals - which can often be neglected in real-world operations - a predictive maintenance approach enables terminal operators to have an overview of the status of every machine in the fleet. In some cases, operational data from the actual machines can even be used to predict a replacement need for spare parts ahead of the planned service interval.
"With the latest generation of machines, it's even more critical to have access to the specialist expertise of the equipment provider," says Alveronn. "Predictive data-driven maintenance makes it much easier to avoid unplanned downtime, while simultaneously extending the lifetime of the equipment. Instead of waiting for something to wear out or break, today we can actually help adjust the customer's processes based on data from individual machines."
Maintaining safety
The first priority for all maintenance operations is ensuring safety. From brakes, twistlocks and spreaders to tyres and wheel bolts, equipment needs to be in faultless working order. Daily routine checks are important, but they are not enough on their own.
"Safety as a basic approach needs to be integrated into every aspect of maintenance operations," notes Svante Alveronn. "As systems become more complex, it's important to understand that their safety needs to be ensured on multiple levels. As a basic example, if you have anti-collision sensors on your equipment, you need to be 100% sure they are actually working. Having a safety system in place but inoperable can be worse than not having the system in the first place, so all these features need to be checked regularly."
Fix it before it breaks
In recent years, Kalmar and other logistics industry solution providers have been moving heavily towards electrification. All-electric and automated machines have created additional demands for maintenance, as new skill sets, tools and certifications are required to maintain, for example, equipment powered by high-voltage grid power. As a result of electrification, many operators who have previously done their own maintenance have been moving towards one-stop service contracts.
In the future, maintenance will be increasingly based on digital connectivity between machines and their support systems. Using data collected from actual operations can help not only improve reliability and avoid unplanned downtime, but also extend the lifetime of components that are replaced regularly. All of Kalmar's new machines are factory-equipped for remote connectivity, but the overall level of digitalisation in the industry is still relatively modest.
"It's all about providing insights on which our customers can take action," says Svante Alveronn. "Maintenance and operational optimisation are always linked. For example, you might find that a particular type of work cycle is wearing out the tyres on your machines prematurely. However, this kind of knowledge is almost impossible to discover without having access to the data from the equipment. So an improvement to your operations will affect your maintenance planning, and vice versa."
"We are already able to collect and utilise a lot of real-time data from our equipment that can help optimise operations while improving safety and reliability," adds Timo Elo. "As we move along, we will be able to build on these solutions to provide our customers with even more insight on how their fleets are utilised – and how we can help them maintain them optimally, whatever their preferred maintenance approach."
DOWNLOADS
Related articles
Further reading
Subscribe and receive updates in your email
Subscribe